We are pleased to announce that, our HF-55M Seamless Flux Cored Wire approved by DNV and 4Y50 grade.
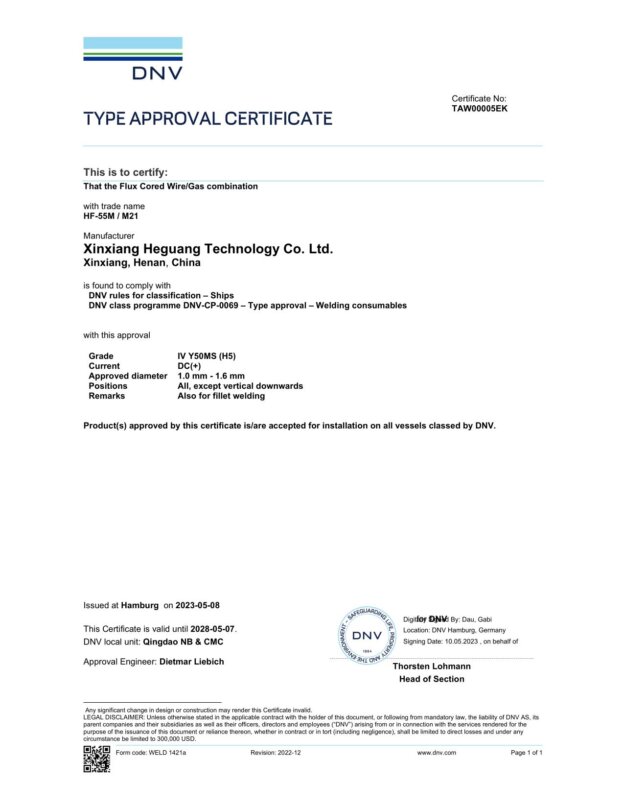
We are pleased to announce that, our HF-55M Seamless Flux Cored Wire approved by DNV and 4Y50 grade.
Within FCAW , seamless cored wires offer optimal protection against moisture reabsorption.
During use, moisture cannot penetrate into the filling since there is no closed seam running over the wire length. This extremely low level of diffusible hydrogen prevents the weld from hydrogen induced cracking or cold cracking.
HG-1F / E71T-1C is a seamless rutile flux cored wire applicable for all-positional welding with
100% CO2 shielding gas.
Thanks to its unique seamless structure, HG-1F / E71T-1C generates low spatter and has excellent impact properties in low temperature.
These properties make HG-1F / E71T-1C the perfect seamless cored wire for industries such as shipbuilding, steel construction, bridges, offshore, pipes, and pressure vessels.
Features & Benefit
HeGuang Technology is a high-tech company dedicated to develop and manufacture Seamless Flux-Cored Wires and Seamless Metal-Cored Welding Wires for shipbuilding, offshore, pipeline, bridge fabrication, structural steel fabrication and other industries. We are China’s AWS A5.29 E81T1-Ni1M-J flux cored wire manufacturer and supplier.
A5.29 E81T1-Ni1M-J is a type of flux-cored wire used for welding. The designation “A5.29” refers to the American Welding Society (AWS) specification for low-alloy steel electrodes for flux-cored arc welding. The “E” in the designation indicates that it is an electrode, and the “81” indicates the minimum tensile strength of the weld metal in ksi (thousands of pounds per square inch).
The “T1” indicates that the electrode has a rutile (titanium dioxide) flux, which provides good weld bead shape and slag release. The “Ni1M” indicates that the wire has a nominal composition of 1% nickel and 0.5% molybdenum, which provides good toughness and resistance to cracking in the weld metal. The “J” at the end indicates that the wire meets the impact toughness requirements when tested at -40°C.
Flux-cored wire is a type of welding wire that contains a flux core, which provides shielding from the atmosphere during the welding process. This allows for welding in outdoor or windy conditions, where solid wire and gas shielding may not be practical. Flux-cored wire is also often used for welding thicker materials, as it can provide deeper penetration than solid wire.
AWS A5.18 E70C-6M is a type of metal cored wire used for welding. Metal cored wires are similar to flux-cored wires in that they have a tubular design, but instead of a flux coating, they have a metal powder filling. This metal powder filling contains various alloys and other materials that help to improve the welding process.
This type of wire is commonly used for welding carbon and low-alloy steels, especially in applications where high productivity and good penetration are desired. The metal powder filling helps to increase the deposition rate, resulting in faster welding speeds and higher productivity. The wire also produces a smooth, low spatter weld with good bead appearance.
AWS A5.18 E70C-6M is a type of welding wire that conforms to the American Welding Society (AWS) specification A5.18. The “E70C-6M” designation indicates the specific type of wire, where “E” stands for electrode, “70” refers to the minimum tensile strength of the weld metal, “C” indicates that it is a composite electrode (i.e., metal-cored wire), “6” refers to Chemical Composition Requirements for Weld Metal from Composite Electrodes, and the “M” means that it is suitable for welding with 75%–80% Ar/balance CO 2 (M21) gas.
Seamless flux-cored wire for hardfacing is a type of welding wire used to create wear-resistant coatings on metal parts. Hardfacing is a process in which a layer of wear-resistant material is applied to a metal surface to increase its durability and lifespan.
Seamless flux-cored wire for hardfacing is designed to be used in applications where a high degree of wear resistance is required, such as in mining, construction, and manufacturing industries. The seamless design of the wire allows for a consistent and uniform deposit of the welding material, resulting in a smooth and uniform surface finish.
The flux in the wire provides shielding from the atmosphere and produces a slag that covers the weld, protecting it from contamination. The hardfacing material is typically made of alloys such as chromium, tungsten carbide, or cobalt-based alloys, which are chosen for their high hardness and wear resistance.
It is important to use the correct type of hardfacing material and welding parameters when using seamless flux-cored wire for hardfacing to ensure a high-quality and long-lasting coating. The manufacturer’s instructions and recommended welding parameters should always be followed for optimal results.
ISO 14700 is a standard developed by the International Organization for Standardization (ISO) that specifies requirements for the deposition of metallic and other inorganic coatings on metallic substrates by various thermal spray processes. This standard covers the following thermal spray processes:
ISO 14700 provides guidelines for the selection of coating materials and their properties, the preparation of substrates, and the control of the thermal spray process. It also covers the testing and evaluation of coatings to ensure that they meet the required quality and performance standards.
The purpose of this standard is to ensure that thermal spray coatings are applied consistently and reliably to provide the required level of protection, such as wear resistance, corrosion protection, or thermal insulation. Compliance with ISO 14700 can help ensure that thermal spray coatings are of high quality and will perform as intended in their intended application.
ISO 14700 is widely recognized as a global standard for thermal spray coatings and is used by many industries, including aerospace, automotive, energy, and defense.
ISO 14700 T Fe8 is a code that refers to a specific type of thermal spray coating material. The “T” in the code stands for “Thermal Spraying,” indicating that the material is intended for use in thermal spray processes, such as flame spraying, plasma spraying, or HVOF spraying.
The “Fe” in the code refers to the primary element in the coating material, which in this case is iron. The number “8” indicates the percentage of the primary element in the material, which in this case is 8%.
Therefore, ISO 14700 T Fe8 specifies a thermal spray coating material that contains 8% iron as the primary element. The specific properties of the coating material, such as its hardness, wear resistance, and corrosion resistance, will depend on the specific composition of the material and the thermal spray process used to apply it.
AWS A5.20 E71T-1C is a type of flux-cored welding wire used for welding carbon steel. It is classified as an all-position welding wire, meaning it can be used for welding in any position, including overhead. The “E” in the name stands for electrode or filler metal, while “71” indicates a tensile strength of 71,000 psi. The “T” signifies that it is a tubular electrode, and the “1” indicates that it is an all-position welding wire. The “C” at the end of the classification designates that it has a Charpy V-notch impact toughness requirement at -30°C.
This type of welding wire is designed to be used with CO2 shielding gas, which provides good penetration and a stable arc. It is commonly used in industries such as shipbuilding, offshore oil and gas, and structural steel fabrication. AWS A5.20 E71T-1C welding wire provides excellent weld bead appearance, easy slag removal, and low spatter levels. It has a high deposition rate, which makes it ideal for welding thicker sections of metal.
As with any welding process, it is important to follow the manufacturer’s instructions and recommended welding parameters when using AWS A5.20 E71T-1C welding wire to ensure a high-quality and strong weld.
AWS A5.20 E71T-1M is a type of welding wire that is used in flux-cored arc welding (FCAW) processes. This welding wire is designed for welding mild and low-alloy steel, such as structural steel, sheet metal, and heavy equipment.
The “E71T-1M” designation indicates the wire’s characteristics, including its tensile strength, welding position, and shielding gas requirements. The “E” stands for electrode, the “71” indicates a minimum tensile strength of 71 ksi, and the “T” refers to the wire’s tubular shape. The “1” indicates that it can be used in all positions, and the “M” means that it is suitable for welding with a mixture of argon and CO2 gases.
This welding wire is often used in construction, shipbuilding, and other heavy fabrication applications. It offers excellent weldability, good mechanical properties, and high deposition rates, making it a popular choice among welders. Additionally, AWS A5.20 E71T-1M welding wire has a low spatter and a smooth arc, which helps to produce high-quality welds.
The main difference between AWS A5.20 E71T-1C and AWS A5.20 E71T-1M welding wire is the classification and intended use.
AWS A5.20 E71T-1C welding wire is designed for welding carbon steel and is classified as an all-position welding wire. The “C” designation at the end of the classification means that it has a Charpy V-notch impact toughness requirement at -30°C.
On the other hand, AWS A5.20 E71T-1M welding wire is specifically designed for welding mild steel and low alloy steels. The “M” designation in the classification means that it has a lower diffusible hydrogen content than the “C” classification. This makes it ideal for applications where hydrogen-induced cracking is a concern.
Both types of welding wire are classified as flux-cored, meaning they have a hollow core filled with flux. The flux provides shielding from the atmosphere and produces a slag that covers the weld, protecting it from contamination.
It is important to note that both types of welding wire should be used in accordance with the manufacturer’s instructions and recommended welding parameters to ensure a high-quality and strong weld.
AWS A5.20 E71T-1M is a type of welding wire that is used in flux-cored arc welding (FCAW) processes. This welding wire is designed for welding mild and low-alloy steel, such as structural steel, sheet metal, and heavy equipment.
The “E71T-1M” designation indicates the wire’s characteristics, including its tensile strength, welding position, and shielding gas requirements. The “E” stands for electrode, the “71” indicates a minimum tensile strength of 71 ksi, and the “T” refers to the wire’s tubular shape. The “1” indicates that it can be used in all positions, and the “M” means that it is suitable for welding with a mixture of argon and CO2 gases.
This welding wire is often used in construction, shipbuilding, and other heavy fabrication applications. It offers excellent weldability, good mechanical properties, and high deposition rates, making it a popular choice among welders. Additionally, AWS A5.20 E71T-1M welding wire has a low spatter and a smooth arc, which helps to produce high-quality welds.
“Seamless” typically refers to a type of steel pipe or tube that does not have a welded seam along its length.
Seamless flux-cored wire is a type of FCAW wire that has a seamless outer sheath or shell, which provides a number of advantages over traditional seamed FCAW wire. Some of the advantages of seamless flux-cored wire include:
Improved weld quality: Seamless flux-cored wire produces a more stable arc and smoother weld bead compared to seamed wire, which can result in higher-quality welds with fewer defects.
Reduced spatter: Seamless flux-cored wire is designed to produce less spatter during welding, which can help to reduce the amount of post-weld cleanup required.
Increased productivity: Seamless flux-cored wire can be run at higher amperages and deposition rates compared to seamed wire, which can help to increase welding productivity.
Enhanced operator comfort: Seamless flux-cored wire produces less fume and smoke compared to seamed wire, which can help to improve operator comfort and reduce the risk of respiratory problems.
Lower total cost: Although seamless flux-cored wire is typically more expensive than seamed wire, its improved quality and productivity can result in a lower total cost of welding by reducing rework, cleanup, and downtime.
Overall, seamless flux-cored wire can offer a number of advantages over traditional seamed FCAW wire, making it a popular choice among welders in a variety of industries.
Seamless flux-cored wire is a type of welding electrode used for welding applications that require a high degree of precision and strength.
The wire is made from a metal core that is coated with a flux material, which serves as a shielding agent to protect the weld from atmospheric contamination. The flux also helps to improve the quality of the weld by providing additional alloying elements and promoting a more uniform distribution of the metal.
One of the main advantages of seamless flux-cored wire is that it allows for high-speed welding with a high deposition rate.
This is because the wire is designed to produce a stable and consistent arc, which helps to minimize the amount of spatter and other defects that can occur during welding. Additionally, seamless flux-cored wire is able to produce a high-quality weld even in adverse weather conditions.
Seamless flux-cored wires fulfills the highest requirements for productivity and quality.It is fabricated for a new area in high duty cycle welding in mechanized and robotic applications to match
the needs of demanding applications.
Let us see benefits of seamless flux cored wires below: